В металлургическом производстве важен каждый этап, но особое значение имеют операции с расплавленным чугуном. На выходе из доменной печи температура чугуна достигает 1500 °C, и с этого момента начинается обратный отсчет. Задача — как можно быстрее доставить его в конвертерный цех с минимальными потерями тепла и без простоев.
Ключевой элемент этого процесса — ковши, которые транспортируют чугун по рельсам. Раньше их перемещение отслеживали вручную — по рации и телефону. Этот подход нес в себе риски: задержки, ошибки, отсутствие информации в нужный момент. Сегодня же эту задачу решает цифровая система на базе RFID-меток. Меня зовут Иван Клестов-Надеев, я главный специалист по цифровизации коксохимического, доменного и энергетического производства НЛМК, и сегодня я расскажу, как мы вместе со специалистами НЛМК ИТ эту систему реализовывали.
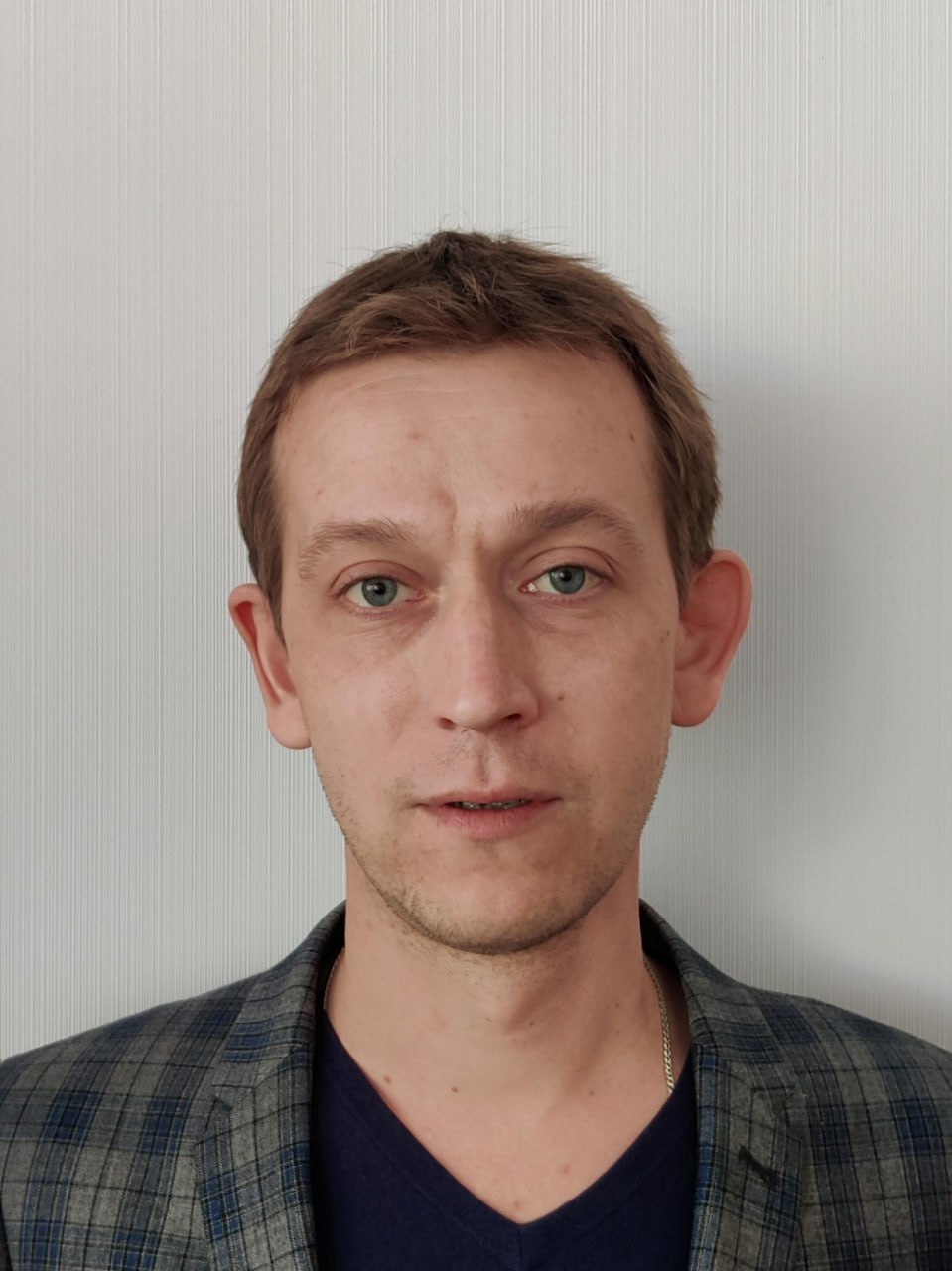
От аналога — к цифре
Для стабильной работы производственной цепочки необходимо точно знать, где в каждый момент времени находится конкретный ковш. Ручной подход не позволял получать информацию оперативно, а в случае отклонений или изменения маршрута реакция часто запаздывала. Это вело к сбоям, нарушению графиков, увеличению простоев, снижению температуры металла и дополнительной нагрузке на оборудование. Результат — финансовые потери.
Поэтому на ряде объектов было принято решение внедрить RFID-технологию и интегрировать ее с цифровой платформой DEM (Digital Enterprise Model, цифровая модель предприятия). Это позволило сформировать непрерывную систему отслеживания ковшей, исключило влияние человеческого фактора и обеспечило прозрачность логистики.
Техническое решение и его особенности
Команда предприятия оснастила каждый ковш шестью RFID-метками. Но из-за высокой температуры внешней поверхности ковша — порядка 150–200 °C — стандартные «коробочные» решения не подходили. Поэтому для надежной работы в условиях металлургического производства использовали жаростойкие метки, размещенные в стальном корпусе с теплоизоляцией. Конструкция корпуса исключает прямой теплообмен с ковшом и защищает оборудование от механических воздействий. Монтаж же выполнялся сваркой — чтобы обеспечить необходимую прочность и долговечность.
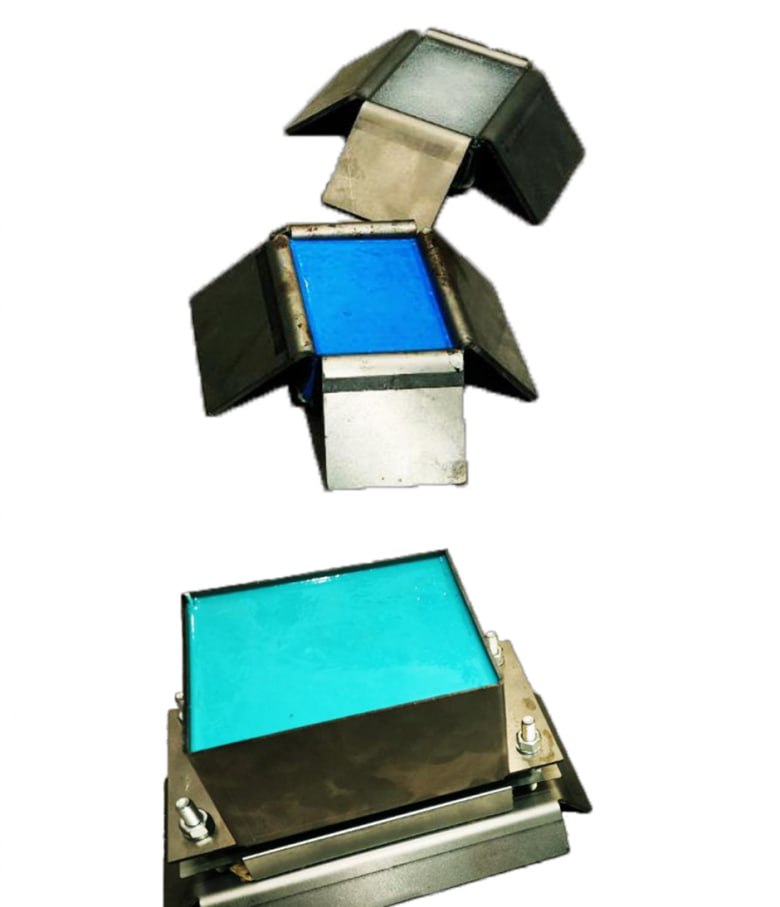
RFID-считыватели с антеннами специалисты разместили в ключевых точках перемещения ковшей — от выхода из доменного цеха до приемки в миксерном отделении, на весах, в депо очистки и ремонта ковшей, на разливочных машинах и пр. Все элементы системы подключены к платформе DEM — она представляет собой виртуальную копию предприятия с возможностью визуализировать технологические маршруты и процессы.
В платформе команда создала цифровую модель участка с нанесением точек контроля и зон идентификации ковшей. Систему также интегрировали с уже существующей ERP. Каждой метке присвоили уникальный идентификатор, связанный с параметрами ковша, — температурой, массой, выпуском, химическим составом, маршрутом движения и рядом других характеристик.
Работа системы не требует участия оператора в процессе считывания. Как только метка оказывается в зоне действия антенны, информация автоматически поступает в систему и отображается на мнемосхеме, или карте. Это позволяет диспетчерам, мастерам и другим участникам производственного процесса в реальном времени контролировать движение каждого ковша и принимать решения на основе актуальных данных.
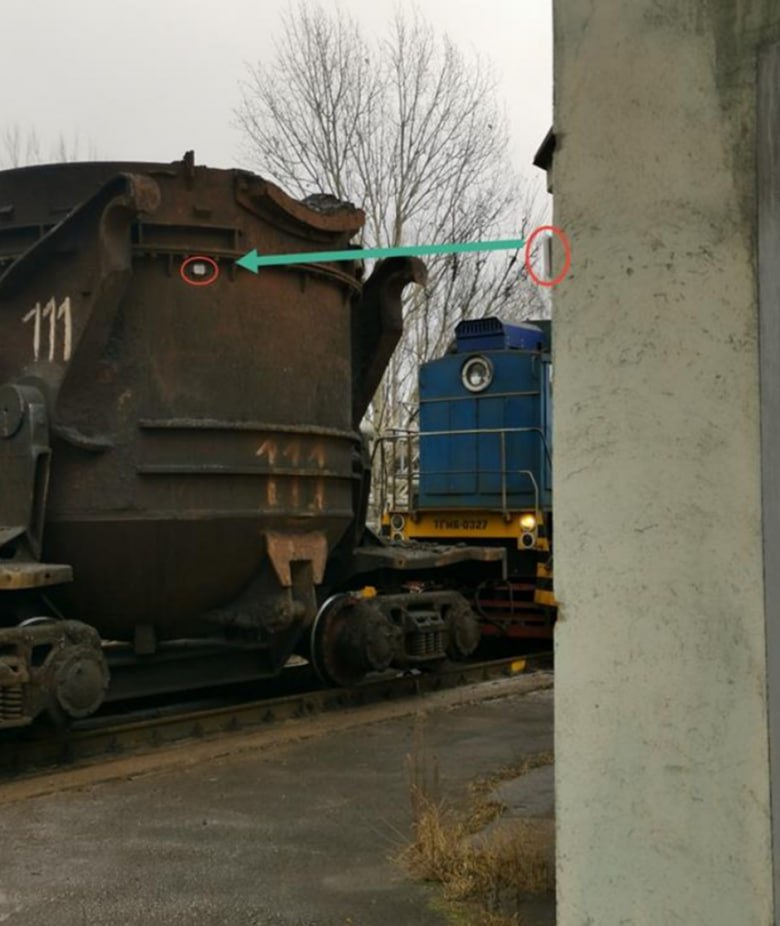
Что в итоге
Использование RFID-меток позволило существенно повысить прозрачность производственного процесса. Ковши перестали теряться, все диспетчерские теперь видят их текущее положение и статус, могут заранее планировать логистику и оперативно реагировать на любые изменения. За счет этого удалось сократить время простоя, снизить теплопотери, оптимизировать загрузку оборудования и улучшить использование ресурса ковшей.
Дополнительно в систему был интегрирован модуль тепловизионного контроля, который позволяет отслеживать наружную температуру ковшей, по которой можно определить состояние футеровки ковшей. Это помогает выявлять перегретые участки и своевременно направлять оборудование на осмотр и ремонт. А вся история движения, состояния и наливов сохраняется в системе — и упрощает таким образом планирование, а также повышает производственную безопасность.
RFID-инфраструктура уже доказала свою эффективность в отслеживании ковшей с чугуном. Однако на этом внедрение не остановилось. Решение применяется, например, для отслеживания транспортировки лома, а команда уже прорабатывает проекты по цифровому контролю сырья в стационарных хранилищах. Гибкость платформы позволяет быстро адаптировать ее под новые задачи и участки, что делает возможным поэтапное масштабирование на другие элементы производственной цепи.
Комментарии